ŠKODA has been selling and distributing spare parts since 1992, when it took over this responsibility from the state-run Mototechna. In the early stages, shipments were distributed straight from the production plant. In May 1998, ŠKODA started building a special warehouse to store genuine parts, the ŠKODA Parts Center, including stock-in and stock-out sites and an office building. Originally a 34,000 m2 facility, the site has gradually grown to its current 105,000 m2 and has become one of the Volkswagen Group’s three central warehousing operations in Europe.
The Center stores 140,000 items, from small screws to big bodywork parts. In total, the warehouses handle over 13 million units of various sizes, which are stored and distributed to service partners and dealers; the supply of parts to production lines is a separate operation.
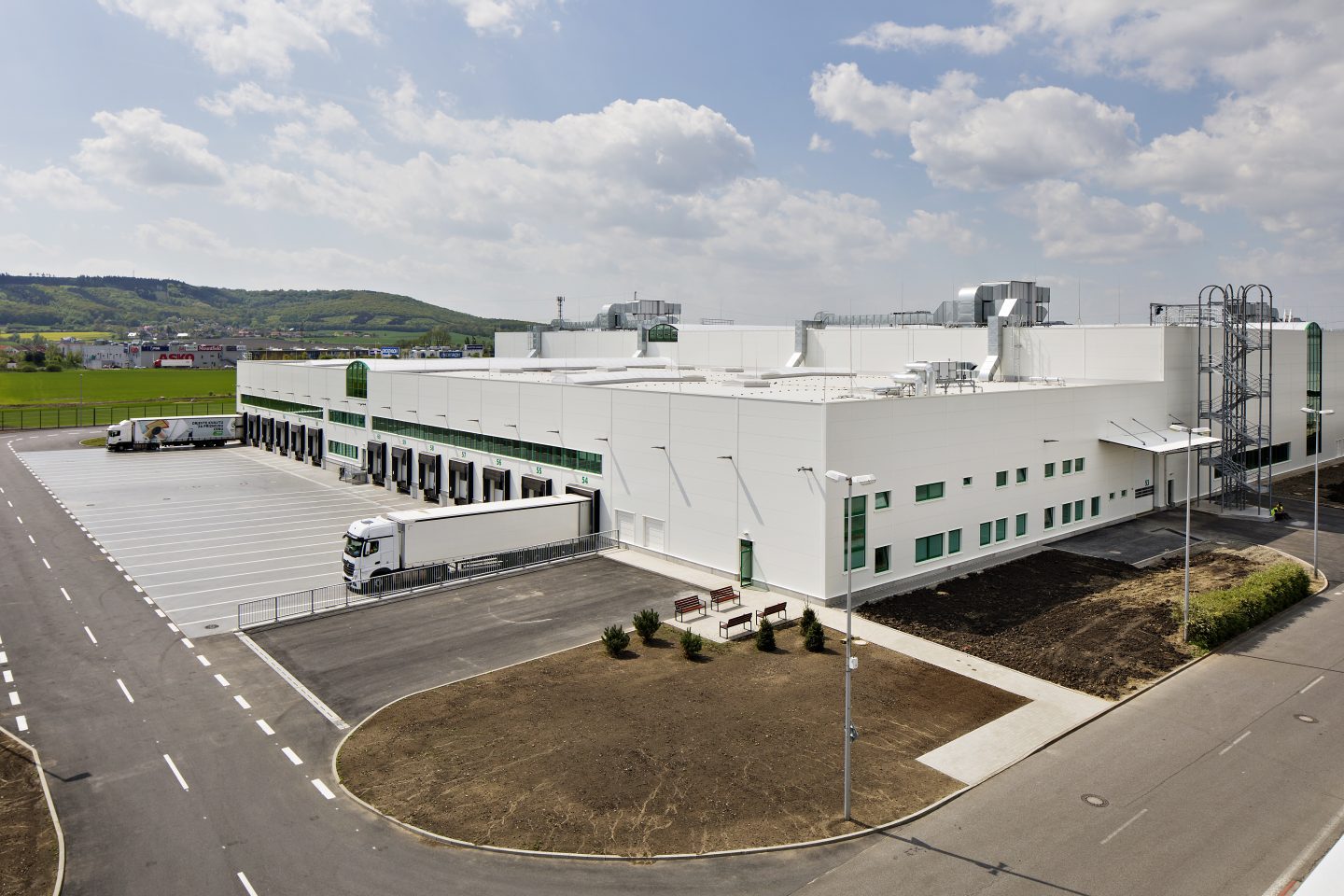